How can we futureproof sterile storage departments, and safeguard patients?
Many hospitals find maintaining proper conditions for sterile storage challenging – something often compounded by insufficient storage space and staff shortages. Sterile Processing Departments across our NHS were designed for the needs of hospitals many decades ago. As staffing levels continue to affect our country’s healthcare provision, and the demands of an aging population increase, we are seeing demand outstrip capacity. Maintaining the integrity of sterilised items is paramount to client safety, as is ensuring quick and accurate access to the appropriate inventory. It is only by ensuring proper storage requirements; that both shelf life, and patient safety can be preserved. Shelf life is heavily influenced by degrees of handling, as well as storage methods. In manual inventory systems, sterile equipment and supplies may are routinely handled several times between goods-in, inventoried, stored and picked for use – providing a number of opportunities for contamination, wear and breakages.
Several issues regularly compromise the shelf-life, integrity, and usability of these items:
- Physical damage to packaging
- Improper or excessive handling
- Items stored in areas with excess moisture or poor circulation
- Over stacking of products in storage areas
- Poor temperature control
Hänel storage systems are renowned for their quality, benefits, and prevalence across health settings the world over. Whether carousel or VLM (vertical lift module), our machines bring items directly to the picker – cutting down on handling, thus lessening risks of contamination. Enormous design variations, such as perforated panels (for excellent air-circulation) as well as cold and freezer boxes, allow departments to store wider varieties of stock in one, central, and dedicated location.
Items are tracked and audited, allowing the health board or hospital to maintain 100% stock transparency, lowering wastage and pilferage, while removing over and under ordering errors. The units ensure greater storage capacity, on a much smaller footprint than any traditional racking or shelving units – allowing you to generate more space for additional stock storage, or to repurpose your newly found space for other critical hospital needs – such as operating rooms, larger A&E capacity or increasingly popular “ready to go” wards.
Better, safer and more efficient storage, with enhanced shelf-life, faster access and 100% stock transparency in hospitals is good for all patient outcomes. Moreover, more efficient, machine picking (GM2) allow hospitals to redeploy staff to other critical areas of hospitals, improving access to fast healthcare across the NHS.
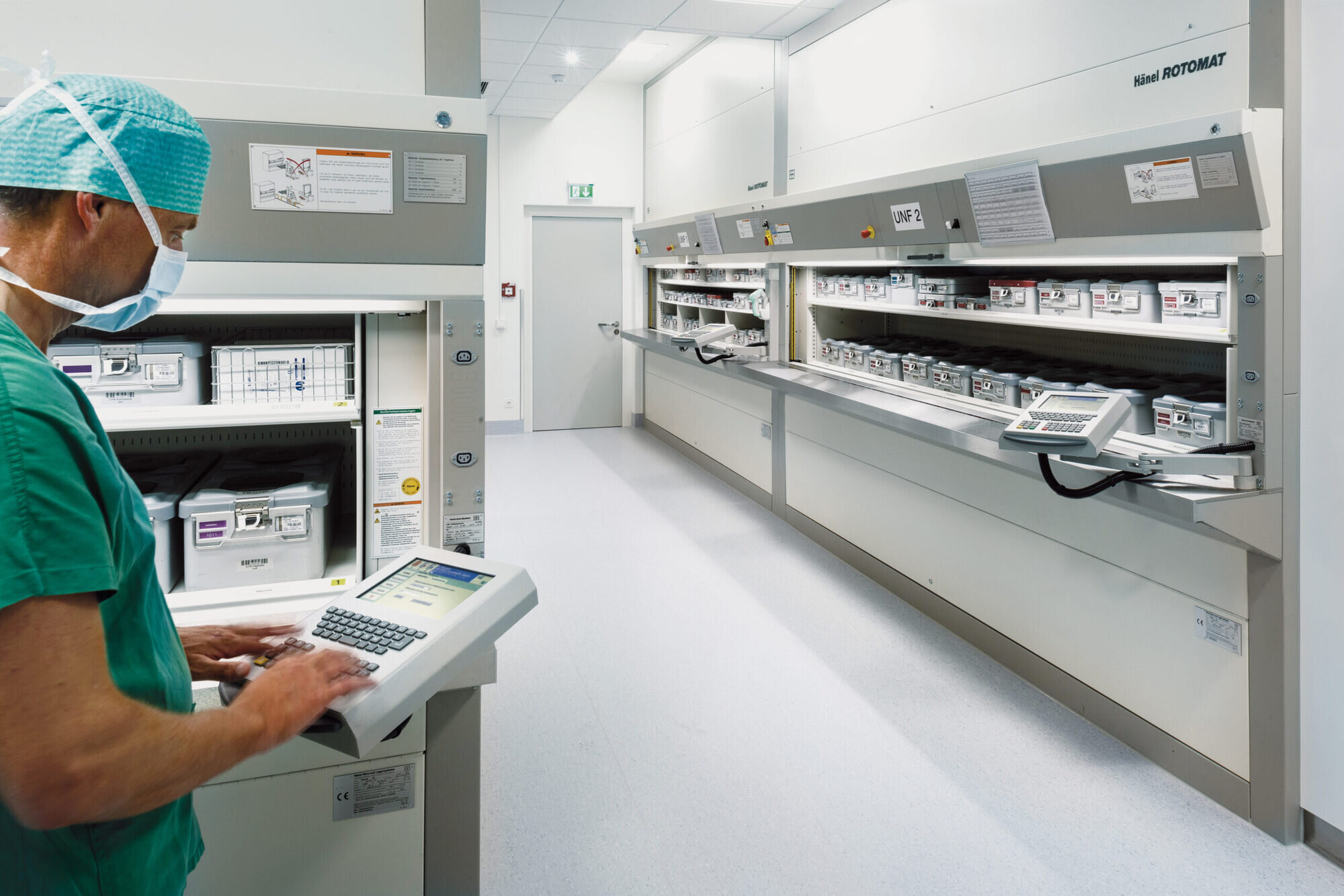