Hyster-Yale Group is a leading, globally recognised forklift truck manufacturer, who will soon be celebrating their centenary. For nearly 100-years, H-YG (Hyster-Yale Group) has been recognised as a pioneer in their industry – and real innovation heavyweights. For the past five-years, they have been harnessing the power of Industore’s Hänel Lean-Lifts to streamline their operations in County Armagh, Northern Ireland.
H-YG faced the same industry challenges as most successful businesses: the need for quicker, more accurate picking, and better use of space, as the company sought to expand. To address these problems, they turned to leading intralogistics experts, Industore. Following a thorough site-audit, completed by Industore’s Irish Sales Director, Trevor Elliott, H-YG opted for Six Hänel Lean-Lifts, packed with state-of-the-art technology – to house their fastest moving small and medium sized components.
Lean-Lifts are renowned for their incredibly dense storage capacities. As well as storing products vertically, thereby utilising the full height of any facility, Lean-Lifts are in a league of their own when it comes to how densely shelves – and therefore items – can be stored in vertical spaces. The head height in H-YG’s Armagh facility is 10-meters, and each of their Lean-Lifts measure 9.986m tall, ensuring maximum height utilisation, and maximum capacity. Mark Topley, Hyster-Yale Group’s Material Superintendent:
Each machine has 60 shelves, and each shelf is the equivalent to two-Euro pallet spaces. That’s huge. The space we’d need were we still using NA [narrow aisle] racking would be enormous – not to mention how much more time we’d spending picking and replenishing.”
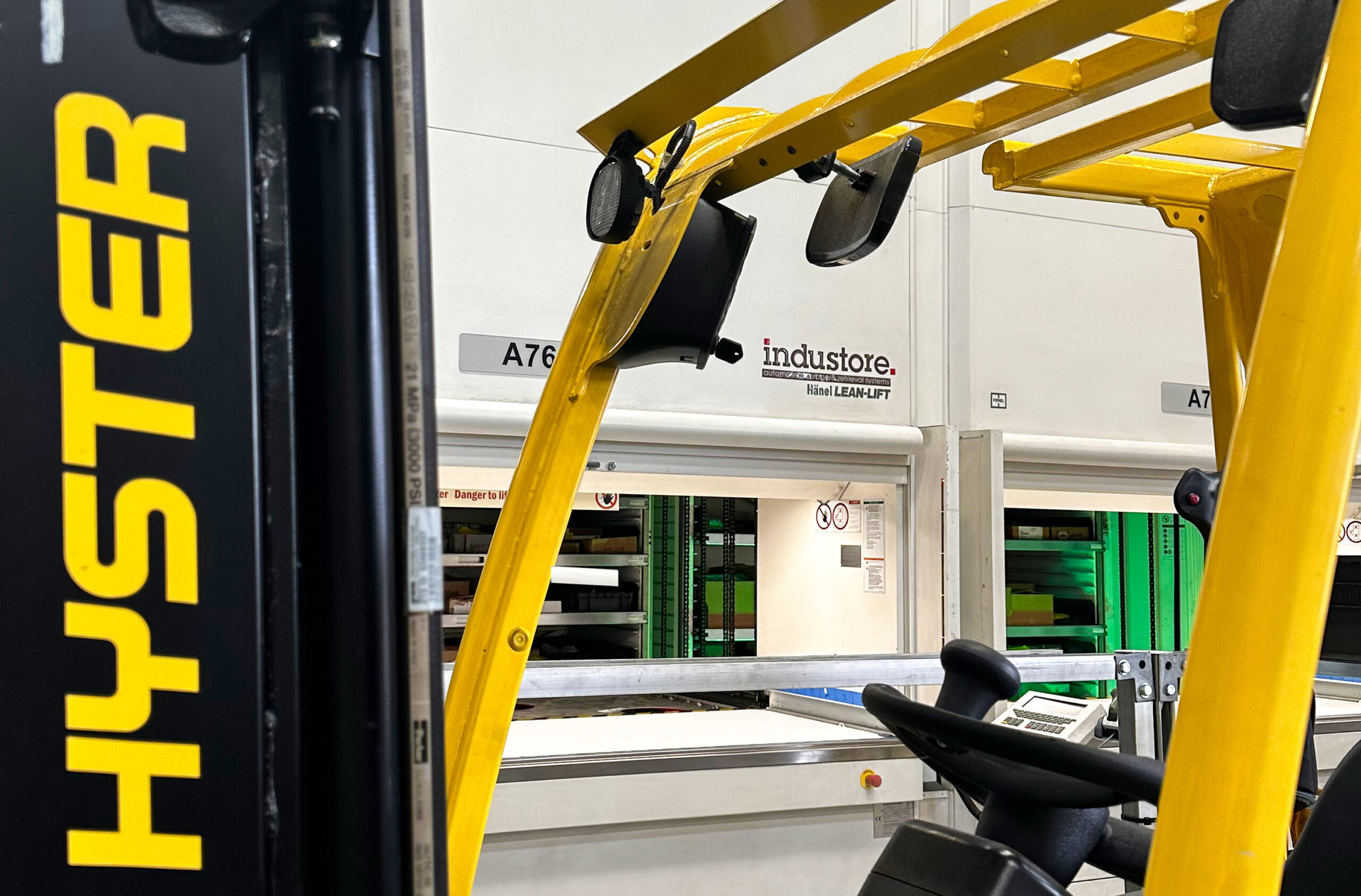
H-YG have managed to repurpose their newly found, former racking spaces to create additional, bulk storage capacity – increasing their stock levels. Perhaps more importantly, since moving to the Lean-Lift system, storage and retrieval times are said to be over three-times faster than their previous narrow aisle racking process. Industore’s solution has also empowered H-YG to achieve the illustrious 100% stock transparency target, as Mark Topley explains:
Access to the lifts is secured with fobs and PINs. Once an operator has finished their shift, or is stepping away from the Lean-Lifts, the machines lock themselves. We also have comprehensive audit logs readily available, and cameras inside the lifts, ensuring total accuracy and accountability. More than that, with the machines, our staff are always picking and replenishing at an ergonomic height. There’s no stretching or reaching, and by extension, there are no broken or missing parts. The lifts also have a lot of sensitive items in them – and inside the lifts, there’s much less dust and disruption – and that’s critical for certain, expensive and/or sensitive items.”
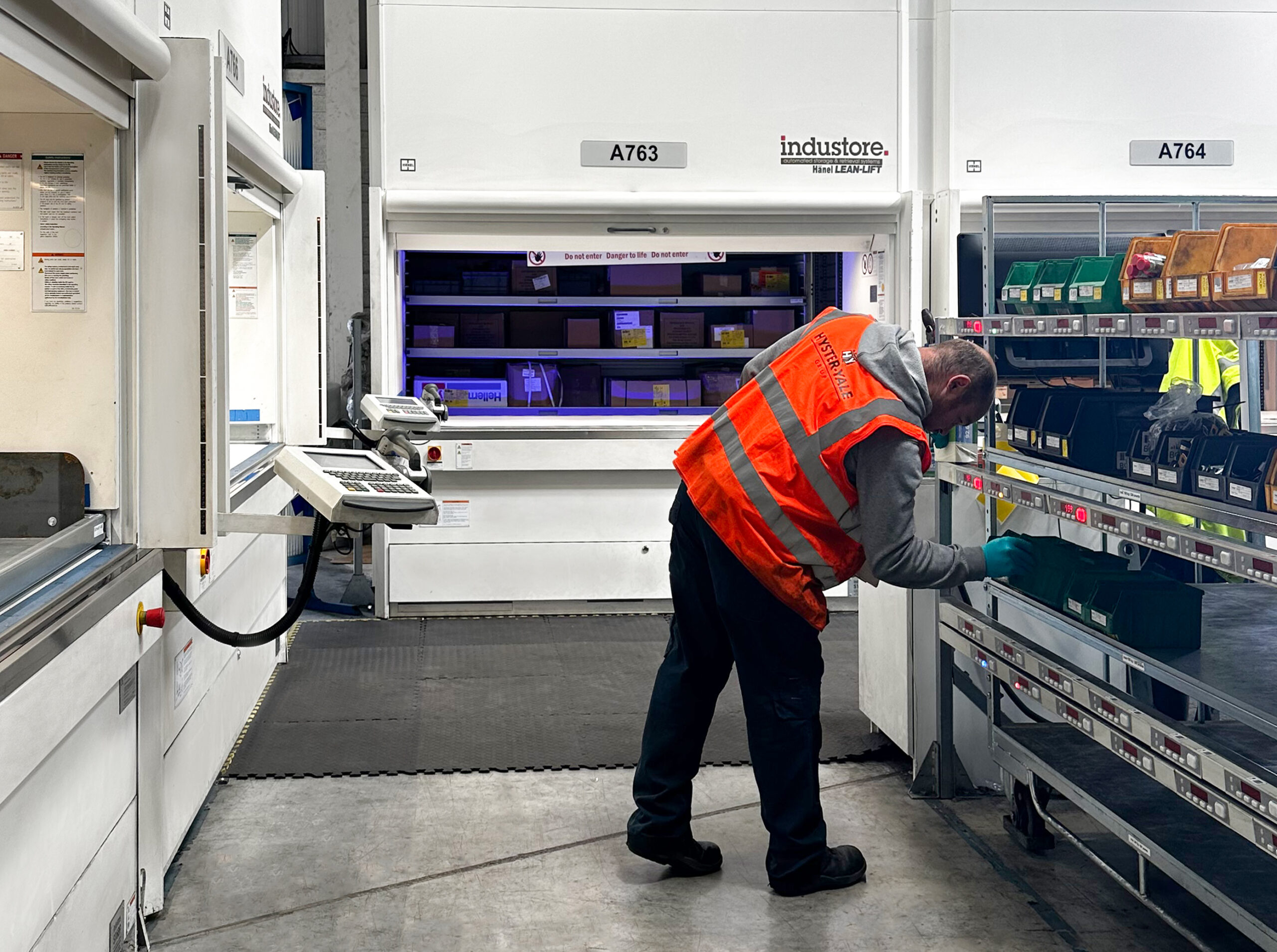
One of the most standout, successful features of H-YG’s transformation is their integration with MPX software. Industore’s expert I.T. teams made light work of the integration, as Software Manager, Stephen Froude explains:
“Industore has never failed to integrate a client’s SAP system into our solutions. It’s an accolade we’re extremely proud of, and another thing that separates us from the crowd in AS/RS circles. The added benefit for H-YG is that the integration has allowed them to batch-pick – which is a much more effective, efficient way of picking and replenishing stock, and it ensures that stock levels can be monitored (by those with appropriate access) from anywhere in the world, giving 100% accuracy and transparency.”
Typically, a Lean-Lift’s return on investment is roughly 20-months. However, H-YG experienced an even quicker payback due to the size of the transformation from their narrow aisle (NA) racking to AS/RS with batch-picking. This investment has not only paid for itself inside a year, but also continues to provide enduring benefits in terms of efficiency, accuracy, and safety.
The collaboration between Hyster-Yale Group and Industore Limited showcases the transformative power of Hänel Lean-Lifts and MPX software in addressing common industry challenges. The Lean-Lifts’ space optimisation, efficiency gains, operator satisfaction, and accountability have made them a valuable asset for H-YG, underlining the significant advantages of integrating Industore solutions into the modern warehouse management process.
Side note: What is batch picking?
Batch picking is an order fulfilment method used in warehouses, distribution, and manufacturing centres to increase efficiency. It involves consolidating multiple customer orders into a single picking process. Industore’s lifts automatically retrieve the appropriate trays from multiple different lifts, ensuring pickers are never waiting for the next item. Pickers need only scan items out of the lifts, and into the appropriate tote. The process continues until all orders are complete, streamlining picking processes, reducing errors, and improving overall productivity. Throughout the process, inventory information is updated in real-time, ensuring 100% accurate tracking of inventory wherever it’s needed.
Mark Topley concludes:
Industore’s machines are incredibly reliable. Other than an initial teething problem at the very beginning (which we later determined to be down to user-error) we’ve never had a problem. That being said, if we did run into any trouble, I have total faith in the Industore team, from our project manager to their service people, right through to the office-staff who manage our aftercare plan. I’d really like to get a few more Lean-Lifts in here because the value they offer is enormous, and it’s something that’s understood by everyone at Hyster-Yale. The operators love them, I love them, and I’ve already recommended them to our supply-chain and other partners.”