Nestled in the natural beauty of Mid-Wales, Montgomery Waters Ltd. sits at the foot of former volcanic hills. Beneath a little rural village in Churchstoke, ancient rock formations have developed a vital passage that host essential minerals, providing Montgomery Waters, with fine tasting natural and spring water.
To ensure total protection of the water, Montgomery Waters has operated on essential areas of land above the source for over 30 years. As product demand increased, modern machinery was introduced to the production line, which resulted in the business expanding significantly, making every inch of the facility’s footprint vital.
In 2016, Montgomery Waters looked to the market for a futureproof storage solution. Ambitious to be one of the UK’s leading water bottles businesses, the company needed a catalogue of critical spare parts for the production line to be stocked on-site, as production down-time would be a costly expense.
Project description:
In the first instance, Montgomery Waters opted for a mezzanine and traditional racking systems to utilise the height of the facility, but soon found inefficiencies while storing and locating variable SKUs (stock keeping units) in static stations.
As a supplier to corporate giants, Montgomery Waters sought advice from likeminded businesses, and was ultimately referred to Industore for their vertical storage solutions. Steve Prosser, Operations Director at Montgomery Waters explains:
“During initial consultation with Industore’s Sales Manager, Steve Anderson-Tyso, we realised our valuable space was wasted with static racking, as there were metres of dead space above our racking. Following a comprehensive audit from Steve, who took time to learn about the business requirements, we opted for the recommended 5.9 meter high Hänel Lean-Lift in a facility which measured just over this, to ensure ease of access if needed in the future. Complete with 50 shelves and clever shelf mapping abilities, we are able to densely store70% of our critical parts on each shelf in less than 10% of our warehouse footprint.
Since installing the Lean-Lift over 7 years ago, it’s ultimately provided us with peace of mind. Full inventory transparency allows us to locate SKUs swiftly, and accurately quantify parts in stock. Stored in a clean-environment and with parts delivered at an ergonomic height, our company has seen a significant decline in part damages and losses. Our critical SKUs range in value from 30p to £10,000 in the automated storage system, ensuring any issues are resolved promptly, allowing our production line to run seamlessly. Our production line is operating 24-hours a day, 6 days a week, and therefore the Lean-Lift is an integral part of safeguarding operations.”
The Hänel Lean-Lift is equipped with various features which improve operations, safeguard staff, add precautionary measures to logistics and day-to-day operations. As a safety precaution, our Hänel Lean-Lifts are equipped with specialised light barriers, which will instantly halt the machine when sensors are triggered. Once instructed on the sophisticated MP 12 N controller, the machine will resume item retrieval when safe to-do so. When Montgomery Waters replenish the Lean-Lift with critical parts, integrated software ensures the shelf is returned to an optimal location, thanks to dynamic storage and precision height detector sensors. The optimisation run module ensures shelves which contain parts frequently requested are stored closer to the Lean-Lifts access point, prompting faster retrieval. To maximise security, a lockable sliding door was installed at the front of the Lean-Lift.
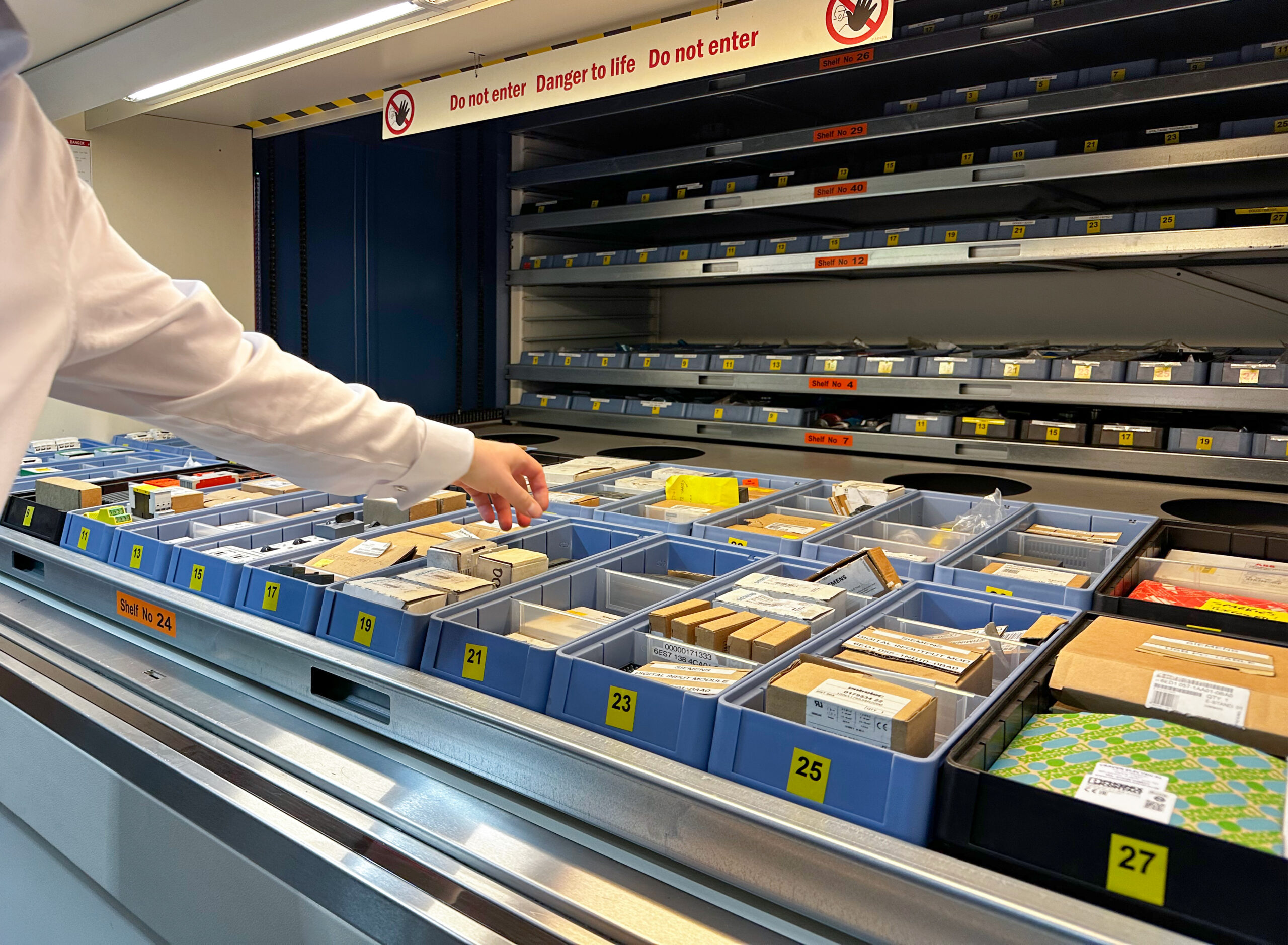
Aftercare:
Montgomery Waters Lean-Lift is storing high value components, integral to the production line, and as such, this forward-thinking client opted for an Industore Aftercare plan. By taking out a Service Contract, the Lean-Lift is serviced annually by a Hänel certified, qualified engineer. In the unlikely event of a breakdown, in-house telephone support is available, and Montgomery Waters will receive priority call outs should the issue persist.
Steve Prosser continues:
“Maximum up-time of the vertical lift is vital, and having the Service Contract presents us with confidence to store our most valued components in one central location. In the 7 years we’ve had the Lean-Lift Installed, we’ve not encountered any issues that couldn’t be very quickly overcome, and these were always down to be simple, human error. It’s a brilliant machine, and the service we’ve had from Industore has been exemplary. We’re currently in conversations with our Sales Manager, Steve, about a second lift – and I wouldn’t hesitate to recommend to others.”