MP 14 N Controller
High-performance control system with 12-inch touch screen Hänel control technology in new dimensions.
The 12-inch high-resolution touch display supports maximum ease of use, allowing plenty of space to show vast amounts of information. This is ideal for the presentation of user interfaces for various ERP systems – directly at the storage system terminal – possible thanks to the integrated SOAP interface.
The fully integrated warehouse management system (WMS) has also been optimized for the large display and improved in terms of functionality and convenience. The MP 14 N uses the latest browser technology to display critical information. Integrating the MP 14 N in existing networks is completed quickly, just as it is with the MP 12 N.
There is no need for a classic alphanumeric keyboard with the MP 14 N – texts are entered using the virtual keyboard displayed directly on the touch screen. When used in conjunction with Hänel PictureControl, the camera feature integrated in the Lean-Lift’, the large display area of the MP 14 N is a great advantage.
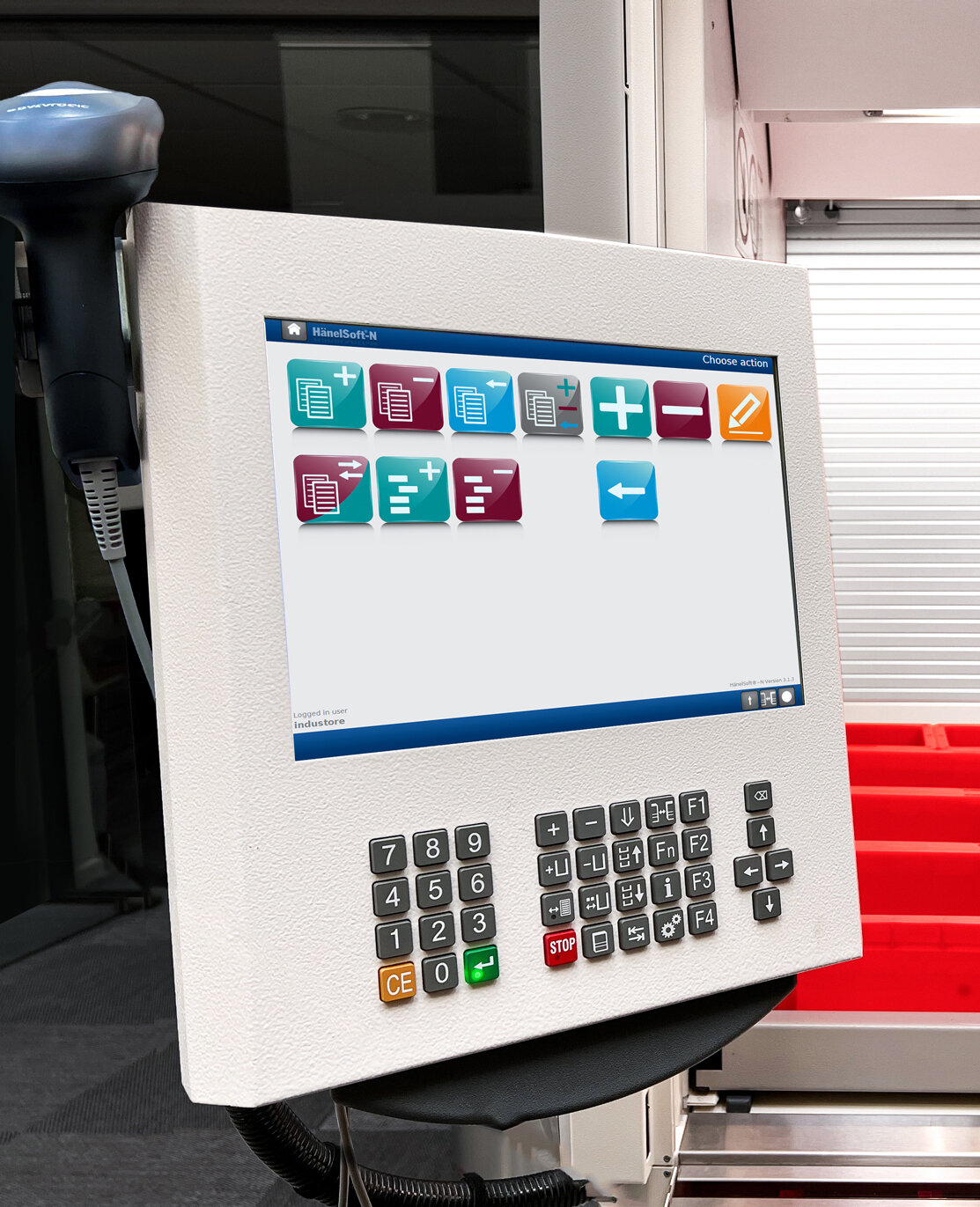
Top features and advantages:
Three operating modes are integrated in the MP 14 N system:
- MP 14 N-StandAlone
- MP 14 N-HostData
- MP 14 N-HostWeb
MP 12 N Controller
One control system, four operating modes. The MP 12 N – the compact controller for Rotomat, Lockomat, Lean-Lift and Multi-Space
Whether you use the Hänel storage systems as stand-alone solutions with integrated inventory management or want to integrate the control units into a higher-level ERP system – the top controller MP 12 N from Hänel has every thing built in as standard.
This is the compact controller for Hänel storage systems with comprehensive, integrated storage management for article numbers, storage locations, stock quantities, minimum inventory and other supplementary data fields.
The many configuration options give the user a tailored range of functions.
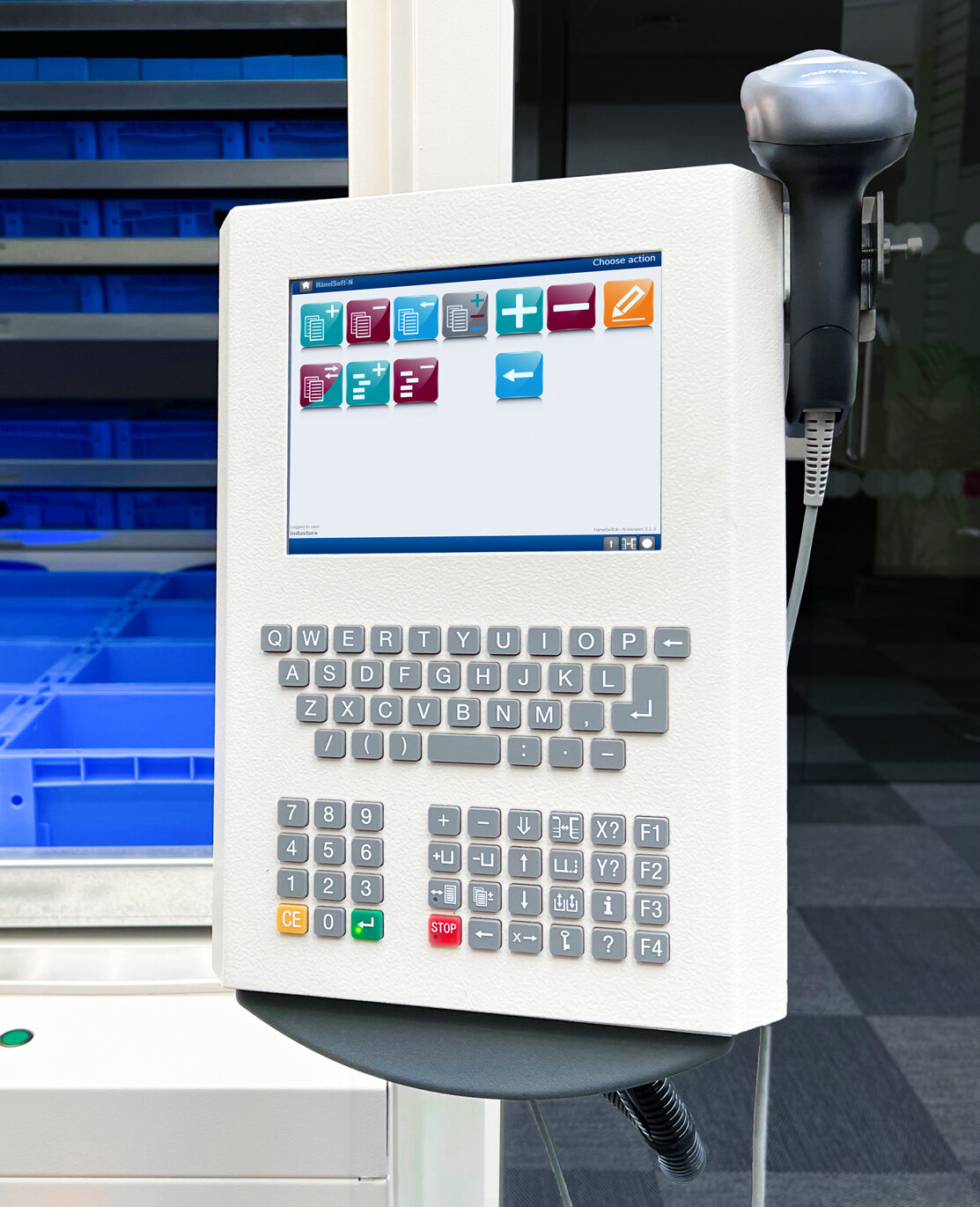
The Hänel advantages:
There are three different operating modes available, so you can choose the right one for your storage management.
- MP12 N-StandAlone
- MP12 N-HostData
- MP 12 N-HostWeb
Software Integration
For many years Hänel’s MP 100 D and MP 12 N-HostData control systems have been supporting data exchange without the need for additional middleware. An FTP server, a Windows drive release or a web service interface is all that is required for data exchange between the Hänel controller and the customer’s ERP system.
Integrated Control Software
The MP 12 N, MP 14 N controllers all have integrated warehouse management functionalities – to learn more about Hanelsoft integration contact us today?
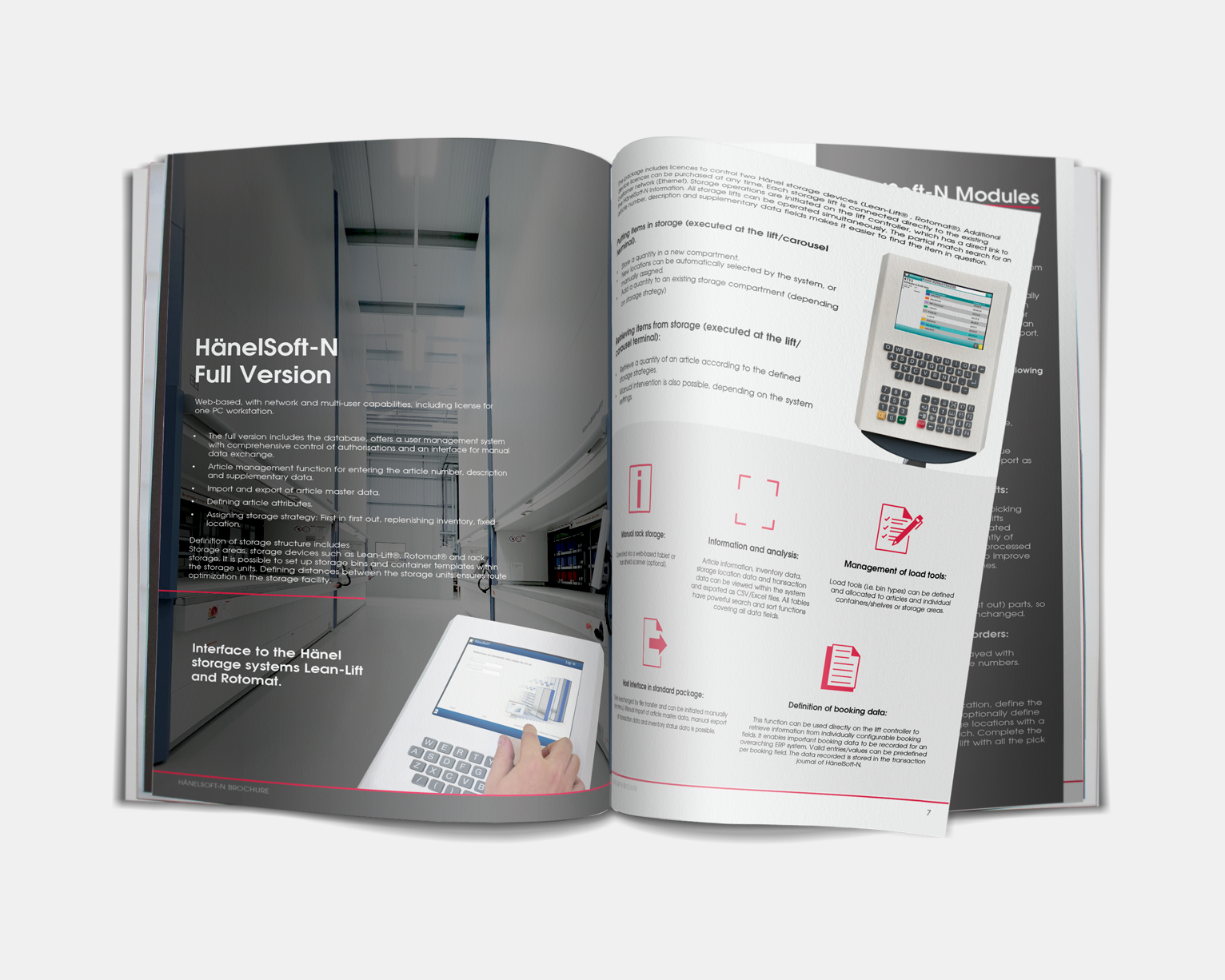
Operating modes:
Standalone
The Standalone mode includes the core functionality of an integrated WMS, including the management of items, locations and stock quantities. This functionality can be expanded through supplementary modules and integration with an ERP for order processing. In this mode, both the software and data reside within the Hänel controller, with no requirement for additional PC hardware. When multiple Hänel machines are used, these can be connected to allow route-optimized processing of orders and a unified interface.
Host-Data
The Host-Data mode includes the core functionality for order processing and requires integration with an ERP/WMS. In this mode, the ERP/WMS manages the items, locations and stock quantities, with the Hänel controller used to process orders transferred via an electronic interface. When multiple Hänel machines are used, these can be connected to allow route-optimized processing of orders and a unified interface.
Host-Web
The Host-Web mode allows the ERP/WMS to control the Hänel machine directly. In this mode, the ERP/WMS manages the items, locations and stock quantities, with the Hänel controller processing shelf movements transferred via an electronic interface. When using this mode, information can also be displayed on the controller via the integrated web browser and a bespoke web application.